Classification of Semiconductors by Supply Risk
Why classifying items is important for a company?
This work could save multi-million on procurement cost and avoid losing multi-billion for order-fulfillment issues.
Different procurement strategy can be made based on Supply_Risk_Category, Procurement_Cost_Category and Demand_Fluctuation_Category.
​

Supply
Risk
Demand
Fluctuation
Procurement
​Cost
Three categories determine a raw material's procurement strategy.
All procurement items are classified from risk, cost, and demand.
Possible procurement management strategies for items in different categories
-
Supply_Risk = High, Procurement_Cost= Low, Demand_Fluctuation = High: Probably a high inventory level is suitable.
-
Supply_Risk = High, Procurement_Cost = High, Demand_Fluctuation = High: Try to lower Supply_Risk, e.g. introducing more suppliers.
-
Supply_Risk = Low, Procurement_Cost= High, Demand_Fluctuation = Low: Keep very low inventory level, e.g. one week.
The challenge: Accurate classification is critical for implementation of these advanced management strategies.
The workflow
We classified 3k items, ~$2 Billion/year, into four categories by supply risk working with supply chain and suppliers
The selected features e.g. number of qualified suppliers, supply capacity, dedicated level, factory geographic distribution, etc

Quantification of each supply-risk is pretty challenging.
​
Take the 'Location' risk as an example.
Fabrication plants at the following locations can be regarded as high-risk:
Part of Japan and Taiwan: Earthquake
Thailand: Flood
South Korea: Political tension was high with N. Korea.
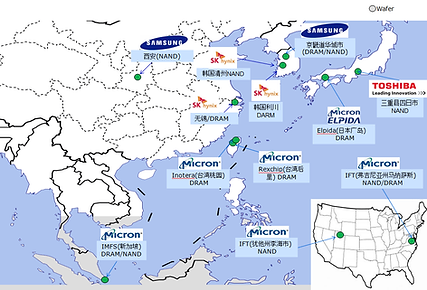
Locations of major memory fabrication plant
How big data can help?
With big-data techniques, it is possible to utilize historic data such as material consumption, daily inventory level, and weekly forecast records to find risky items. We may also be able to find whether a material's supply risk is increasing or declining.